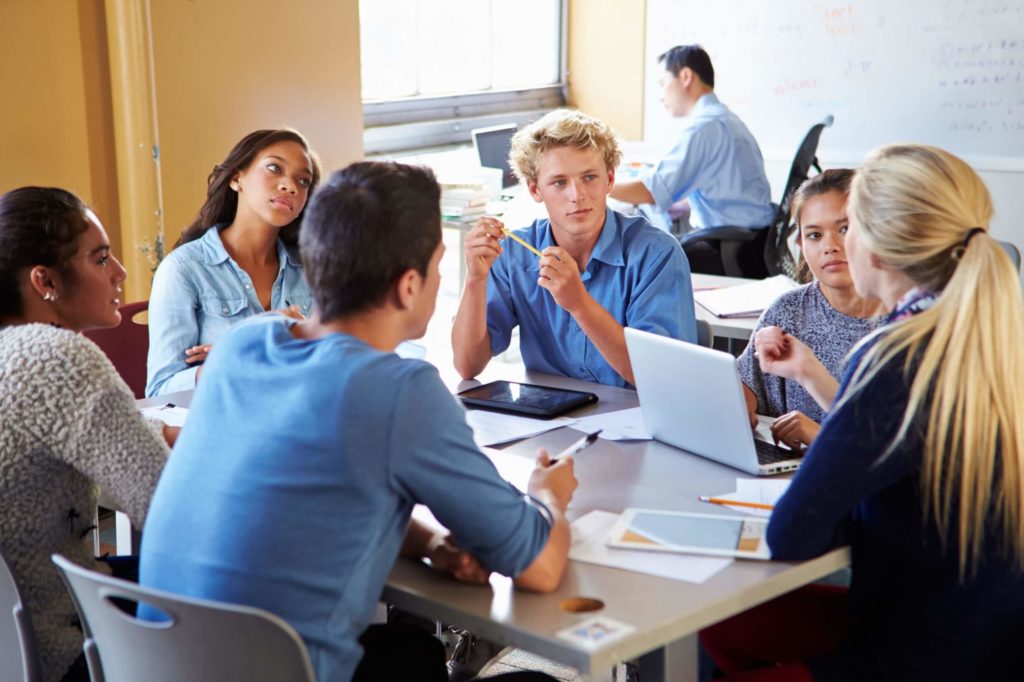
1.Requirement Insight and Planning:
The team first focused on the in-depth analysis of existing products and the exploration of actual user needs. This involved applying knowledge from both engineering and non-engineering disciplines. On this basis, the team assessed these engineering problems and identified constraints such as cost, technical feasibility, and space limitations, which were clearly stated in the project brief.
A detailed project plan, including a timeline and task allocation, was formulated to ensure the orderly progress of the project. Each member was clear about their responsibilities and time nodes, laying a solid foundation for subsequent design and development work, which reflects effective teamwork and individual responsibility.
2.Design Concept and Selection:
After determining the project objectives, multiple design concepts were explored for each key function. Evaluated in multiple dimensions such as cost, accuracy and versatility, this demonstrates the ability to apply engineering design techniques and consider commercial and industrial constraints.
Determined the most feasible and advantageous design direction. In the process, creativity was used to the fullest extent to establish innovative engineering design solutions and to justify the chosen options.
3.Prototype Construction and Implementation:
According to the selected design scheme, the physical prototype was built. Starting from the construction of the hardware architecture, various electronic components and mechanical parts, and display screens, were carefully selected and assembled, and a reasonable circuit connection was designed to ensure the operation of each component. This requires the application of engineering knowledge and skills, as well as consideration of factors such as cost and manufacturability in commercial production.
Corresponding software codes were written to drive each hardware module and control the functional logic. Step-by-step transformation of design blueprints into actual working product prototypes, reflecting the integrated application of engineering technologies.
4.Testing, Optimization, and Feedback:
After the prototype was built, a comprehensive test of the product was carried out. A detailed test plan and standards were formulated for each function module, and the performance of the product was evaluated through a large amount of experimental data, demonstrating the ability to conduct practical and simulation tests of design solutions.
Based on the test results, user feedback was collected. These feedbacks came from not only ordinary users but also professionals, covering aspects such as functions, operation experience, and safety, providing an important basis for subsequent improvements and promoting the continuous optimization of the product. At the same time, it also reflects the importance and inclusiveness of different user groups’ opinions.
5.Summary, Improvement, and Outlook:
Based on the test results and user feedback, a systematic summary of the project was carried out. The advantages and disadvantages of the product were sorted out. Practical improvement measures were proposed, demonstrating the ability of continuous design improvement.
At the same time, it looks forward to the future application scenarios and market prospects of the product, clarifies the great potential of the product in the public sector, provides direction for further R&D and promotion, and pushes the product to develop in the direction of being more mature and more in line with the market demand, which embodies the ability to control and plan the project as a whole.
Evaluate the environmental and societal impact of solutions to complex problems (to include the entire life-cycle of a product or process) and minimise adverse impacts.
Identify and analyse ethical concerns and make reasoned ethical choices informed by professional codes of conduct.