All-terrain Crawler-type Stair-Climbing Automatic Tracking Vehicle
2023-2024
Mianzhi.Wu Xi.Feng
Tianming.Zhou Yifei.Yin
Guangning.Luo
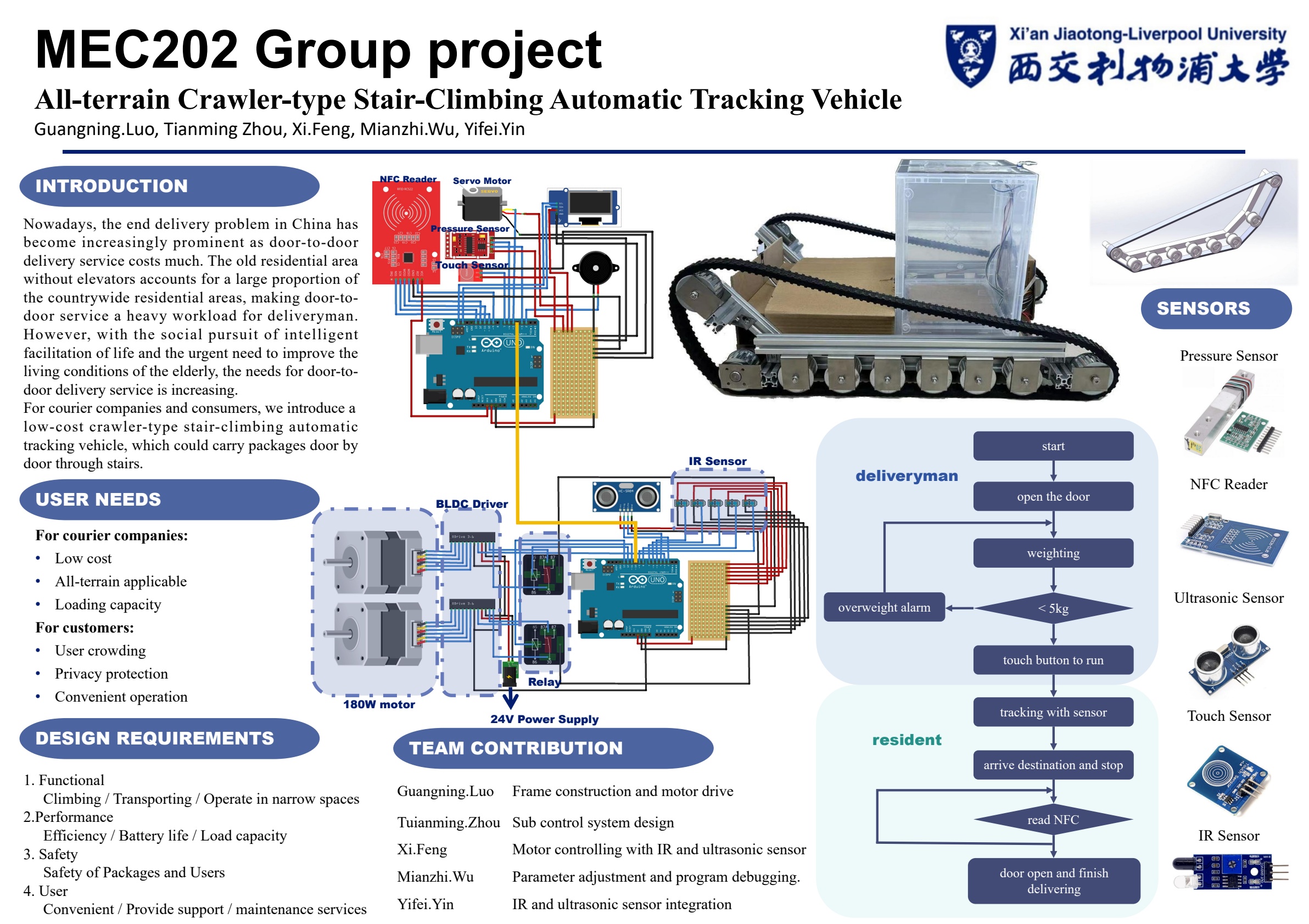
Project Background and Objectives
Background: The last-mile delivery problem in China is prominent. Old residential areas without elevators make it difficult for couriers to deliver packages door to door, while the demand for door-to-door delivery services is increasing. Existing unmanned delivery vehicles have limitations in achieving real door-to-door delivery, and vertical transport robots suitable for buildings without elevators also have deficiencies.
Objectives: To develop an all-terrain crawler-type stair-climbing automatic tracking vehicle that can realize unmanned package transportation from the courier station to the user’s home, solving the problems of delivery companies and users. It should have features such as low cost, all-terrain applicability, appropriate load capacity, privacy protection, and convenient operation.
Design Concepts and Screening
Design Features: Low cost (the total manufacturing cost is no more than 6000 yuan). The aluminum alloy frame ensures strength and is easy to modify, and the crawler design enhances stability. All-terrain applicability is achieved with the help of ultrasonic and infrared sensors. High load capacity, with a 70W motor and special rubber tracks capable of carrying heavy packages. User crowding is avoided and door-to-door delivery is realized through a tracking system and infrared sensors. NFC card identification is used to protect privacy. Convenient operation is achieved through various sensors and a simple structure for automatic door locking and unlocking and convenient package pickup.
Prototyping and Testing
Physical Model Construction
Vehicle Frame: Aluminum profiles are selected. After several design improvements, support wheels, appropriate gears, and driving devices are added to solve problems such as rubber track deformation, component connection, and installation. Finally, a stable vehicle frame prototype is completed.
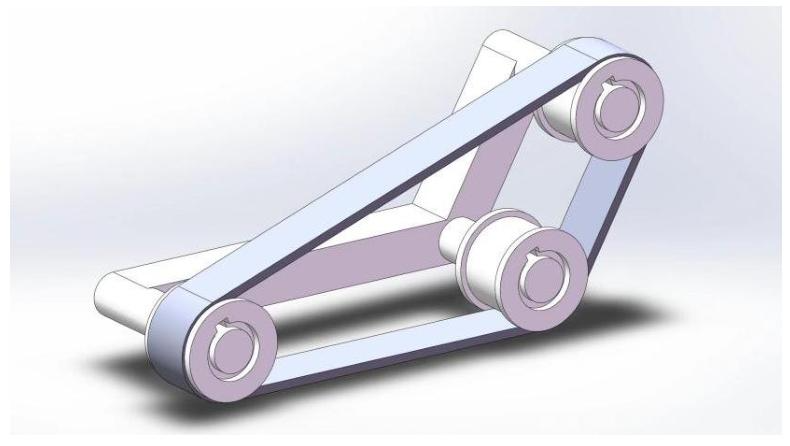
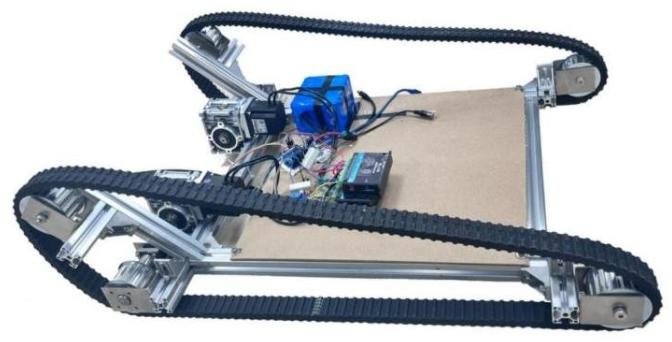
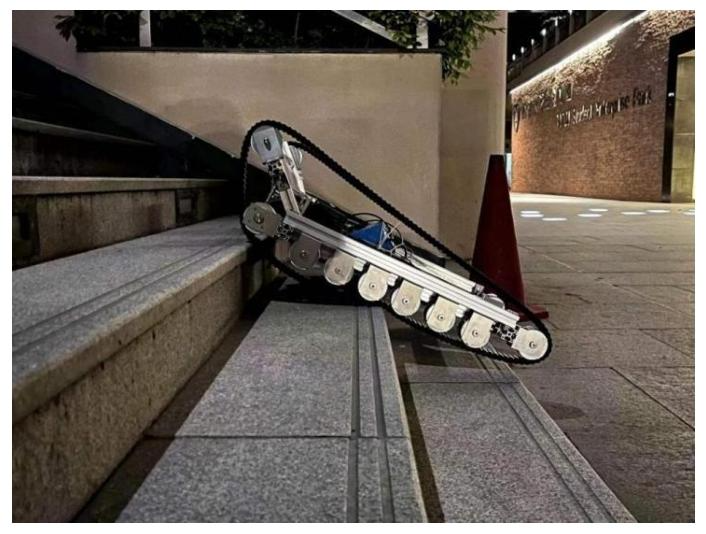
Locker: It consists of weighing, touch, OLED display, steering gear, and buzzer modules, realizing functions such as safe storage of items, overload alarm, automatic door locking, and identity verification.
UNO Board and Sensor Control and Interconnection
Sensor Control: Ultrasonic sensors are used for obstacle avoidance, infrared sensors for tracking, pressure sensors for measuring weight, touch sensors for operation, and NFC sensors for identity verification.
Function Block Interconnection: Various sensors and function modules are connected and controlled through the UNO board to achieve collaborative work.
Testing and Analysis
Test Results: In vehicle operation, the climbing ability on slopes and stairs meets the design requirements, and the collision prevention function is effective. In automatic path tracking operation, the infrared sensors enable the vehicle to travel along the predetermined trajectory. In the intelligent cargo retrieval function, weighing, touch start, and NFC pickup functions all work normally.
User Feedback: Twelve people were invited for testing. Most of them recognized the design function and innovation, but also pointed out problems such as the loud noise of the vehicle when climbing stairs, cost and maintenance. At the same time, they expressed their expectations for load capacity and price.
Future Work: To address the problems of vehicle frame stability and sensor performance, it is planned to improve the vehicle frame by using cast iron or aluminum CNC machining and replace the existing sensors with lidar and OPENCV vision modules.
Project Summary
Product Conclusion: The vehicle developed using Arduino UNO has realized automatic transportation and distribution functions. Sensor integration ensures navigation and environmental adaptability. Although basic functions have been demonstrated, further improvements are still needed. It is expected to have an important impact in the field of intelligent mobile robots in the future.
Social Impact: Automatic delivery vehicles may change logistics and social life, improving delivery efficiency, reducing environmental impacts, and promoting social equity. However, they also face challenges in technology, cost, law, and ethics.
Innovation and Reflection: The project design is innovative, but there is room for improvement in sensor technology, stair adaptability, safety and privacy, load capacity, and long-term operation. Continuous improvement can make it a better solution.